I. Performance requirements and core characteristics of marine exploration and oil exploration cables
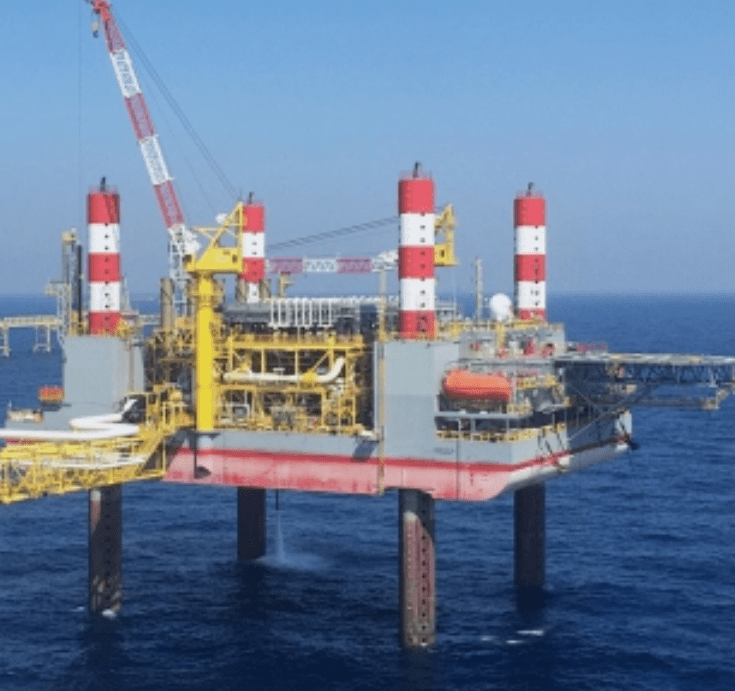
The environment of marine exploration and oil exploration is complex, and the cables need to have the following properties:
- High flexibility and fatigue resistance
Dynamic bending life: It must meet more than 10 million repeated bendings (such as drag chain systems) to adapt to high-frequency mobile scenarios such as drilling equipment and sensor arrays.
Small bending radius: Supports bending with a diameter less than 3 times the outer diameter of the cable to meet the wiring requirements of narrow spaces.
- Corrosion resistance and weather resistance
Material selection: Polyurethane (PUR) or thermoplastic elastomer (TPE) sheath, resistant to seawater corrosion and salt spray (ASTM B117 standard ≥2000 hours).
Temperature range: -40°C to +120°C (short-term up to +150°C), adapting to deep-sea low temperatures and land high temperatures.
- Mechanical strength and wear resistance
Tensile strength: ≥500N (2 cores), ≥800N (4 cores), suitable for high-stress scenarios such as offshore lifting and dragging.
Wear test: passed the Taber abrasion test (CS-10 wheel, wear amount <20mg after 5000 times), ensuring long-term use without damage. - Electrical performance
Insulation resistance: ≥500MΩ/km (20°C), withstand voltage test ≥3kV/1 minute.
Shielding requirements: tinned copper wire braided shield (coverage ≥85%) or aluminum foil + copper mesh composite shield to suppress electromagnetic interference (EMI). - Sealing and waterproofness
IP protection level: IP68 (can be immersed in water for a long time), the terminal seal uses silicone rubber or liquid silicone to prevent moisture and salt spray penetration. - The core advantages of TST CABLES marine exploration and oil exploration cables
- Adapt to extreme environments
Resistant to seawater corrosion, ultraviolet radiation, salt spray erosion and deep-sea high pressure (some models can withstand >10MPa).
Excellent resistance to oil pollution (mineral oil, hydraulic oil) and chemical media (acid and alkali solutions). - Dynamic reliability
The special twisted structure (ultra-fine oxygen-free copper conductor + short pitch twisted) improves the ability to resist torsion loss and avoids signal interruption.
Tear-resistant agent is added to the sheath material to prevent leakage or short circuit caused by mechanical damage. - Lightweight and easy to install
The low-density polyurethane sheath is used, which is 30% lighter than the PVC sheath, which is convenient for offshore platform wiring.
The modular design supports quick replacement and reduces downtime for maintenance. - Environmental protection and safety
Comply with RoHS and REACH regulations, and the halogen-free flame retardant material is UL 94 V-0 certified.
The fireproof performance meets IEC 60332-1-2 (vertical combustion self-extinguishing).
III. Applicable standards and certifications
- International standards
IEC 60092 (marine electrical equipment): specifies the mechanical, electrical and weather resistance of cables in marine environments.
API SPEC 2C (offshore drilling equipment): cable selection requirements for oil exploration equipment.
ASTM D2240 (rubber hardness test): verifies the wear resistance and elasticity of sheath materials. - Industry standards
SY/T 6736.2-2008 (technical conditions for offshore digital seismic acquisition tow cables): applicable to the structure and performance specifications of hydrophone tow cables.
GB/T 51190-2016 (submarine power cable design specifications): guides the laying and protection design of submarine cables. - Special certifications
DNV GL (Norwegian Classification Society): certification for offshore oil and gas platform cables.
CCS (China Classification Society): Meets the cable access requirements for operations in Chinese waters.
IV. Selection recommendations
- Select by core number and purpose
2-core cable: Suitable for simple signal transmission (such as pressure sensors, acoustic wave detectors).
3-core cable: Commonly used for power and signal composite transmission (such as power supply + data feedback for small drilling equipment).
4-core cable: Suitable for complex control systems (such as multi-channel sensor arrays, remote operation equipment). - Key parameter matching
Voltage level: 2-core/3-core ≤600V, 4-core ≤1000V (adjusted according to equipment power requirements).
Conductor cross-sectional area:
2-core: 0.5mm²~1.5mm² (signal transmission);
3/4-core: 1.5mm²~4mm² (power transmission).
Bending radius:
Dynamic application: ≥3×cable outer diameter;
Static application: ≥5×cable outer diameter. - Environmental adaptability design
Deep sea scenario: choose armored cable (steel belt/wire armor) to enhance pressure resistance.
High temperature scenario: use fluororubber sheath (temperature resistance up to +200°C).
Severe electromagnetic interference scenario: double-layer shielding structure (aluminum foil + tinned copper wire braid) is preferred. - Supplier qualifications and services
Choose manufacturers that have passed ISO 9001 certification, such as TST CABLES, and can provide third-party test reports (such as EN, CE, CRCC).
Require suppliers to support customized production (such as special length, color coding, terminal adaptation).
V. Typical application scenarios

- Ocean exploration
Sonar array wiring: 2-core signal cable connects underwater acoustic wave sensors, and the pressure resistance must be >10MPa.
ROV (remotely operated vehicle) control line: 4-core cable transmits power and control signals, and the tensile strength must be ≥800N. - Oil exploration
Drilling equipment power supply line: 3-core cable is used to power the drill motor and needs to be resistant to high temperature (+120°C) and wear resistance.
Subsea seismic acquisition system: 2-core towline is used for hydrophone data transmission and must meet the SY/T 6736.2 standard. - Offshore platform
Lighting and communication line: 4-core cable integrates power and Ethernet signals and supports PoE++ power supply (30W).
VI. Precautions
- Avoid misselection of ordinary cables: Ordinary silicone cables (such as YGG) have insufficient mechanical properties and are not suitable for dynamic drag chains or deep-sea high-pressure scenarios.
- Test verification: Before purchasing, require the supplier to provide a dynamic bending test report (such as 10 million times without breakage) and a salt spray test report.
- Installation specifications:
Reserve 10% redundant length for dynamic wiring to avoid excessive stretching.
Use a special cable clamp to fix it to prevent torsional stress concentration.
2/3/4-core high-flexibility, fold-resistant and wear-resistant cables for marine exploration and oil exploration need to take into account dynamic reliability, environmental adaptability and electrical performance. TST CABLES recommends that you match materials and structures according to specific working conditions (such as temperature, pressure, and corrosion) when selecting, and give priority to products that meet international standards (IEC, API) and industry specifications (SY/T, GB/T). Through scientific selection and strict testing, the operating efficiency and safety of equipment can be significantly improved. If you need marine or oil exploration cables, please feel free to contact TST CABLES by email at any time, and you can also get free samples.
Also available in:
English