Low Smoke Zero Halogen (LSZH) multi-core charging cables are designed for high safety requirements such as electric vehicles, hybrid vehicles and rail transit. They are environmentally friendly, flame retardant and high temperature resistant. The following is a detailed analysis of low smoke zero halogen cable information based on the TST cables cable knowledge base:
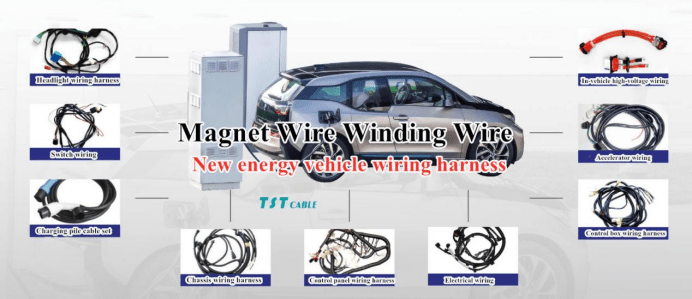
- Core characteristics and advantages
(1) Materials and environmental protection
Low smoke zero halogen materials:
The insulation layer and sheath are made of halogen-free (fluorine-free, chlorine-free, bromine-free, etc.) polymers. When burned, they release very little smoke (transmittance ≥ 60%) and no toxic gases (PH value ≥ 4.3, conductivity ≤ 10μS/mm), which significantly reduces the harm to the human body and the environment during fire.
It meets the requirements of international standards (such as IEC 60332-1, GB/T 19666-2005) for low smoke zero halogen cables.
(2) Flame retardant and fire-resistant performance
Flame retardant grade:
Passed the bundled combustion test (such as GB/T 18380), reaching the A/B/C flame retardant grade, which can effectively inhibit the spread of flames.
Some models (such as WDZN-KYJY) also have fire resistance (fuse does not blow for 90 minutes at 750°C), meeting the power transmission needs in emergency situations.
(3) Temperature resistance and mechanical properties
Working temperature range:
Generally -40°C to +90°C (some models can reach +105°C or higher), adapting to extreme climatic conditions (such as high-cold areas or high-temperature environments in the engine compartment).
Mechanical strength:
Multi-strand stranded bare copper conductors (such as WDZ-DCKPJ-100 cable) improve flexibility, and sheath materials (such as cross-linked polyolefins) enhance wear resistance, tensile strength and impact resistance, suitable for vehicle vibration and dynamic bending scenarios.
(4) Multi-core structure and signal compatibility
Multi-core design:
Single cable integrates multiple conductors (such as WD-MKYJYP33-6×0.75 is 6 cores), supports the coexistence of power lines and signal lines, simplifies wiring and reduces interference.
Shielding layer:
Aluminum foil/copper mesh shielding (such as WDZ-KYYRP cable) is used to block electromagnetic interference (EMI) and ensure signal transmission stability.
- Typical structural design
Take TST cables WDZ-DCKPJ-100 as an example:
Component Material Function
Conductor Multi-strand twisted bare copper wire Low resistance (such as 0.75mm² conductor DC resistance ≤26Ω/100m), high conductivity.
Insulation layer Low smoke halogen-free flame retardant material Flame retardant, high temperature resistant (-40°C to +90°C), in line with UL 94 V-0 vertical burning level.
Shielding layer Aluminum foil/copper braid (optional) Suppresses electromagnetic interference and improves signal integrity (such as characteristic impedance 100±15% Ω).
Sheath Special flame-retardant low-smoke halogen-free polyolefin Oil-resistant and corrosion-resistant (passed salt spray test IEC 60068-2-11), high mechanical strength (tensile strength ≥ 12MPa).
- Application scenarios
(1) Electric vehicle charging system
Onboard charger (OBC): connects the power battery and the charging pile to transmit large current (rated voltage of 300V/500V).
Fast charging/slow charging interface: must meet the GB/T 18487.1-2015 standard to ensure safe and efficient charging process.
High-voltage battery management system (BMS): multi-core cable simultaneously transmits power and control signals (such as temperature and SOC monitoring).
(2) Rail transit
EMU/subway: used for power system (traction motor power supply), control system (signal transmission) and lighting equipment.
Comply with EN 45545 standard: R23/R24 fire protection level of low-smoke halogen-free cable to ensure the safety of passenger evacuation.
(3) Industrial equipment
Hybrid engineering machinery: oil-resistant, vibration-resistant, and adaptable to complex working conditions.
New energy buses: stable operation in high temperature environments (such as engine compartment temperature up to +105°C).
- Key technical standards
Standard category Standard number Main requirements
Material and combustion performance GB/T 19666-2005 Specifies the flame retardant, low smoke, and halogen-free gas release requirements of low-smoke halogen-free cables.
Electrical performance GB/T 3956-2008 Conductor resistance, power frequency withstand voltage (such as 3000V/5min without breakdown) and other tests.
Mechanical performance GB/T 2951.11-2008 Tensile strength, low-temperature impact (-15°C winding test) and other tests.
Electromagnetic compatibility IEC 61180-2-2014 Shielded cable transfer impedance (e.g. 50mΩ/m@1MHz) and near-end crosstalk attenuation (≥65dB@1MHz) tests.
Rail transit EN 50268-2:2011 EMU cable fire resistance (750°C/90min) and smoke density (light transmittance ≥60%) requirements. - Selection and installation points
(1) Selection recommendations
Voltage level: Select 300V/500V or higher (e.g. WDZ-KYJY22 steel belt armored cable) according to charging power.
Number of cores and cross-section:
Power line: single-core or dual-core, cross-section ≥4mm² (e.g. WDZ-DCKPJ-100);
Signal line: multi-core (e.g. 6-core WD-MKYJYP33), cross-section 0.5~2.5mm².
Shielding type:
For high-frequency signal lines, double-layer shielding of aluminum foil + copper mesh is preferred (such as WDZ-KYYRP);
For power lines, single-layer copper braided tape shielding can be selected.
(2) Installation precautions
Bending radius: ≥10 times the outer diameter of the cable (such as WD-MKYJYP33-6×0.75 bending radius ≤10D).
Grounding: The shielding layer must be reliably grounded (grounding resistance ≤4Ω) to avoid the formation of a “pigtail effect”.
Environmental adaptability:
For high-temperature areas (such as the engine compartment), choose a high-temperature resistant model (+105°C);
For humid or corrosive environments, install a waterproof connector (IP67 protection).
- Market trends and low-smoke halogen-free cable manufacturer cases
(1) Market growth
Driven by new energy vehicles: China’s low-smoke halogen-free cable market is expected to reach RMB 18.5 billion in 2025 (Knowledge Base [9]), of which on-board charging cables account for more than 30%.
Policy support: EU RoHS directive and China’s “new infrastructure” policy promote environmentally friendly cables to replace traditional PVC cables.
(2) Typical manufacturers
TST cables:
Product: WDZ-DCKPJ-100 low smoke halogen-free charging cable, voltage 300/500V, temperature -40°C to +90°C.
Advantages: Multi-strand twisted conductor (good flexibility), UL 94 V-0 flame retardant certification.
Tianlian Cable:
Product: WD-MKYJYP33-6×0.75, characteristic impedance 100Ω, suitable for vehicle signal transmission.
Advantages: Aluminum foil shielding + gray sheath, in line with EN 50264 coaxial cable standards.
TST cables low smoke halogen-free vehicle multi-core charging cable has excellent performance in safety (low smoke halogen-free, flame retardant), reliability (high temperature resistance, anti-interference) and environmental protection (halogen-free) through material innovation and structural design. When selecting, you need to consider the voltage level, number of cores, shielding requirements and environmental conditions, and strictly follow relevant standards (such as GB/T, IEC) to ensure the long-term stable operation of electric vehicles and rail transit systems. If you need low-smoke, halogen-free and flame-retardant cables for rail transit, please send an email to contact us and you can also get free samples.
Also available in:
English