PI (polyimide) cables can be divided into two types: extruded and wrapped, depending on the manufacturing process. They have significant differences in material properties, structural design, performance and application scenarios. TST cables makes a detailed performance and test comparison analysis of PI (polyimide) extruded cable and PI (polyimide) wrapped cable:
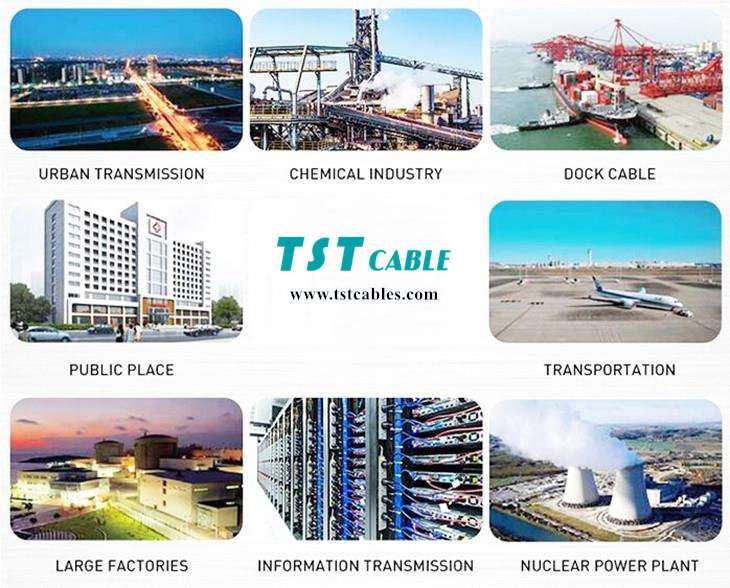
- Process and structural differences
(1) PI extruded cable
Process:
The polyimide material is heated and plasticized by an extruder, and then continuously coated on the wire core to form a dense insulation layer or sheath.
Features:
Good structural continuity, no joints, and smooth surface.
Suitable for high-precision insulation layer thickness control (insulation wall thickness 0.23~0.37 mm).
Usually a single-layer structure, but composite functions (such as flame retardant + wear resistance) can be achieved through multi-layer co-extrusion.
Structural example:
Conductor: silver-plated copper wire (high-conductivity silver-plated copper wire conductor).
Insulation/sheath: PI material is directly extruded, without gaps (fluororesin-coated polyimide composite film is wrapped and sintered).
(2) PI wrapped cable
Process:
The polyimide film tape is wrapped around the wire core by mechanical wrapping, and then fixed by sintering or bonding.
Features:
Multi-layer structure, there may be slight gaps between layers (such as “insulation protection between turns of wrapped wire”).
The wrapping density and number of layers can be flexibly adjusted (such as “multi-core cable: twisted pair, three-core twisted, four-core twisted”).
Additional treatment is required for interlayer bonding (such as “wrapping and sintering” to eliminate gaps).
Structural example:
Conductor: silver-plated copper wire (such as “high-conductivity silver-plated copper wire conductor”).
Insulation layer: polyimide film tape is wrapped + sintered, and other materials may be superimposed (such as PTFE coating).
- Performance comparison
Performance dimension PI extruded cable PI wrapped cable
Continuity and density Continuous without joints, the insulation layer structure is dense. There may be gaps between layers in multi-layer wrapping, and the density needs to be enhanced by sintering or bonding (such as “wrapping sintering”).
Temperature resistance is usually -90°C to +380°C, and some models can reach +400°C (“-269℃-400℃”). It also has a wide temperature range tolerance (-90°C to +200°C), but the interlayer joints may affect the extreme temperature stability.
Mechanical strength The extruded layer has high overall strength and excellent tensile and compressive resistance (penetration resistance and scratch resistance). The wrapping structure enhances the mechanical strength by stacking multiple layers (such as “cutting resistance”), but the interlayer bonding is the key.
Dielectric properties Low dielectric constant (<3.5), low loss (10^-10), and stable insulation performance. It also has low dielectric constant and loss, but the gap between layers may introduce local discharge risk.
Processing flexibility The process is complex and it is difficult to adjust the eccentricity (such as the disadvantage of “extrusion type extrusion” mentioned in [7]. The wrapping process is flexible and the number of layers and density can be quickly adjusted (such as “simple operation of extrusion type”).
Cost and efficiency The extrusion process is efficient and suitable for large-scale production, but the equipment investment is large (such as “fast extrusion speed” mentioned in [7]. The wrapping process equipment cost is low, but there are more manual or semi-automatic operations, and the production efficiency is relatively low.
- Application scenario comparison
(1) PI extruded cable
Typical applications:
Aerospace: Flight control systems that require continuous high insulation performance (such as “high temperature performance of 300°C or higher”).
Electronic equipment: Internal wiring of precision instruments (such as “high temperature cable insulation layer”).
Railway transportation: Lightweight, high heat-resistant cables required by the EN 50264 series of standards (such as TST CABLES high temperature cable products -200℃~1400℃).
Advantages:
Suitable for scenarios with high requirements for insulation continuity and surface smoothness (such as high-frequency signal transmission).
Thin-wall design (such as insulation wall thickness 0.01mm~0.35 mm) can reduce weight and meet the lightweight requirements of aerospace.
(2) PI wrapped cable
Typical applications:
Suitable for medium and low voltage motors with low insulation thickness requirements.
Suitable for products with low performance requirements and cost sensitivity.
Advantages:
Enhanced mechanical protection (such as “cutting resistance”) through multi-layer wrapping.
Flexible adaptation to complex structural requirements (such as multi-core twisting, shielding layer integration).
- Selection recommendations
Requirement Recommended type Reason
High continuity insulation Extruded PI cable No seams, reducing the risk of partial discharge (the sheath and the core are tightly combined without gaps).
Lightweight and thin-wall design Extruded PI cable The extrusion process can achieve an ultra-thin insulation layer (such as 0.01~0.35 mm wall thickness).
Large-scale standardized production of extruded PI cables The extrusion process is highly efficient and fast, making it suitable for mass production.
- Summary
PI extruded cables:
With continuity, density and lightweight as its core advantages, they are suitable for high-precision, high-frequency signal transmission and aerospace and other scenarios with strict requirements on insulation performance.
Comparison of performance advantages of PI extruded cables
- Core advantages of extruded PI copper wires
(1) Ultra-thin insulation and high power density
The thickness of the insulation layer can be 0.08mm or less (minimum 0.20mm for wrapped type), and the conductor ratio is increased by 30%-40% under the same cross-sectional area, significantly improving the power density of the motor and reducing resistance and temperature rise.
Low dielectric loss characteristics (tanδ<0.02%) reduce high-frequency losses and are suitable for 800V high-voltage systems.
(2) More stable performance
Extruded PI wires have a uniform and dense insulation structure, which reduces the risk of partial discharge and has more stable performance in high-frequency, high-voltage or high-vibration environments.
(3) Corona resistance and aging resistance
Nano-scale fillers (such as Al₂O₃, SiO₂) are embedded in the polyimide matrix, with a PDIV value of more than 1500V and a corona resistance life of more than 1000 hours (wrap type is usually <500 hours). Pinhole-free continuous structure, still stable at high temperature (380℃), PDIV attenuation rate <5% (wrap type attenuation after high temperature aging>20%).
High compressive strength
The insulation layer of extruded PI copper wire is dense and has no air gaps. The breakdown voltage is about 15-25% higher than that of the wrap type, which is especially suitable for high-voltage inverters, high-speed rail traction motors and other scenarios.
(5) Mechanical reliability
Tensile strength >350MPa (wrap type is about 200MPa), no cracks after 25% stretching, adapting to the high-frequency vibration environment of the motor.
The bending radius can reach 3 times the conductor size (wrap type usually requires more than 6 times), suitable for compact motor windings.
(6) Better insulation adhesion
The extruded PI copper wire is an insulating layer formed under greater pressure, so it has a tighter bonding, and its insulation performance will not be affected even when it is twisted or bent to produce a large deformation.
(7) Smooth surface and scratch resistance
The insulation layer density of the extruded PI copper wire is higher, the surface smoother, and the scratch and impact resistance is improved by 30-50%; it is suitable for vibration environments such as automobiles, high-speed railways, and aerospace.
(8) Wide temperature range adaptability
The operating temperature range is -269℃~380℃ (the wrapped type is mostly -250℃~260℃), which can meet the needs of ultra-low temperature refrigeration equipment in aerospace.
(9) Better environmental adaptability
Due to the dense structure of the extruded insulation layer, it is more effective in resisting oil pollution and acid and alkali corrosion, and its service life is extended by about 20% in harsh environments such as chemical industry and ships. Since there is no volatilization of residues between the wrapped layers, it is suitable for semiconductor manufacturing and spacecraft vacuum environments.
Clean and environmentally friendly
Extruded PI copper wire has a single material and high purity. It does not contain other harmful substances in either the production process or the use scenario, and is highly environmentally friendly; the wrapped type cannot meet special environmental protection requirements due to the presence of adhesive layer materials.
PI wrapped cable:
When choosing, you need to comprehensively consider factors such as temperature range, mechanical stress, insulation continuity and production cost, and weigh them in combination with specific application scenarios.
TST CABLES extruded polyimide copper flat wire is irreplaceable in the field of high-end equipment (such as new energy vehicles, high-speed rail, and aerospace). Its ultra-thin insulation, high reliability and wide temperature range characteristics are the core driving force for technological upgrading; the wrapped type maintains cost advantages in the mid- and low-end markets and special repair scenarios. In the future, with the popularization of 800V high-voltage systems and wide bandgap semiconductors, extrusion technology will further dominate the high-end electromagnetic wire market. If you need extruded PI cables, please email us and you can also get free samples.
Also available in:
English