In the “heart” system of modern electrical equipment, polyimide (PI) insulated copper wire is like a “blood vessel”, responsible for transmitting power and signals, and its performance directly affects the quality and efficiency of electrical equipment. Traditional wrapped PI copper wire has excellent high temperature resistance, electrical insulation and other properties, but there are still many problems such as high use and maintenance costs, poor wear resistance, and limited application in certain specific scenarios.
In view of the shortcomings of traditional wrapped PI copper wire, TST cables deeply explores the potential advantages of polyimide, a high-performance polymer material, and uses a completely different manufacturing process to maximize its performance. The innovatively launched extruded polyimide insulated flat copper wire can be called the king of cost-effectiveness in the electromagnetic wire industry, crushing the traditional wrapped PI copper wire in all aspects. Today, TST CABLES will explain in detail——
TST CABLES extruded PI copper flat wire
Production efficiency and quality strength crushing
Melt extrusion: Extruded PI flat copper wire is to melt PI resin at high temperature and directly coat the copper conductor through a screw extruder to form a molecular-level dense structure.
No interface stratification: The insulation layer and the conductor are seamlessly combined to eliminate the micro air gap caused by interlayer bonding in the wrapping type (the air gap is prone to cause partial discharge).
Production efficiency: The fully automated continuous production mode is adopted, and the production speed can reach 10-50m/min. It can achieve high-quality large-scale mass production.
Traditional wrapping PI copper wire
Film stacking: The PI film is wound on the conductor surface in multiple layers, and the film is bonded by high-temperature sintering (300℃+).
Interface risk: The interlayer bonding force is weak, the stacking tolerance is large (±0.05mm), and stratification or volatile residues are prone to occur at high temperatures.
Production efficiency: During the production process of wrapped PI copper wire, manual reel replacement and adjustment of the overlap rate are required, and the production speed is about 10-15m/min. Production efficiency and product quality are greatly affected by human factors.
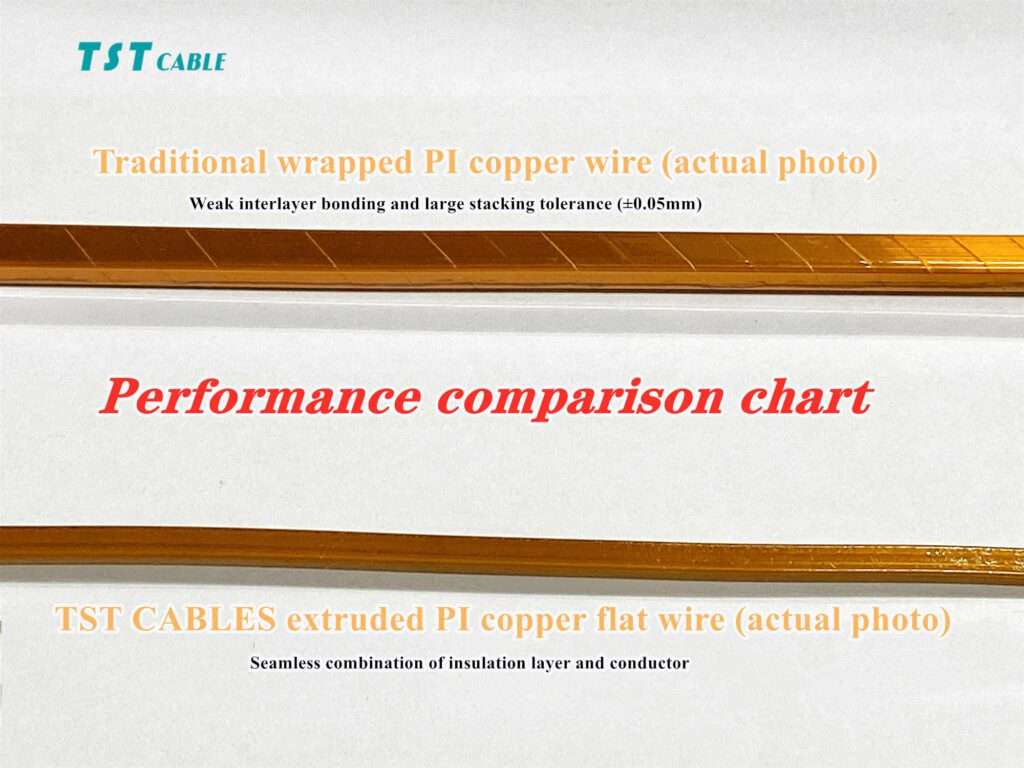
TST CABLES extruded PI copper flat wire has leading performance in all aspects
Ultra-thin insulation and high power density
The insulation layer thickness of extruded PI copper wire can be 0.08mm or less, while the minimum thickness of wrapped type is 0.20mm. Under the same cross-sectional area, the conductor ratio of extruded PI copper wire increases by 30%-40%, significantly improving the power density of the motor, reducing resistance and temperature rise. In addition, its low dielectric loss characteristics (tanδ<0.02%) can effectively reduce high-frequency losses and adapt to 800V high-voltage systems.
More stable performance
The uniform and dense insulation structure allows extruded PI wire to perform well in high-frequency, high-voltage or high-vibration environments. This structure greatly reduces the risk of partial discharge and ensures the stability of electrical performance. Whether inside a high-speed motor or in an environment with strong electromagnetic interference, extruded PI copper wire can reliably transmit power and signals.
Corona resistance and aging resistance
By embedding nano-scale fillers (such as Al₂O₃, SiO₂) in the PI matrix, the PDIV value (corona initiation voltage) of extruded PI copper wire is as high as 1500V or more, and the corona resistance life exceeds 1000 hours, while the wrapped type is usually less than 500 hours. Its pinhole-free continuous structure can remain stable at high temperatures (380℃), and the PDIV attenuation rate is less than 5%, while the attenuation of the wrapped type after high-temperature aging is greater than 20%. In contrast, extruded PI copper wire can work for a long time, high load, and high stability.
High compressive strength
The insulation layer of the extruded PI copper wire is dense and has no air gaps, which makes its breakdown voltage about 15-25% higher than that of the wrapped type. This high compressive strength makes it particularly suitable for use in high-voltage inverters, high-speed rail traction motors and other scenarios with extremely high pressure requirements, and can effectively ensure the safe operation of the equipment.
Mechanical reliability
The tensile strength of the extruded PI copper wire is greater than 350MPa, while that of the wrapped type is about 200MPa. After undergoing 25% stretching, the extruded PI copper wire will not crack and can adapt well to the high-frequency vibration environment of the motor. In addition, its bending radius can reach 3 times the conductor size, while the wrapped type usually requires more than 6 times, which makes the extruded PI copper wire more suitable for compact motor windings to meet the development needs of miniaturization and lightweight of modern electrical equipment.
Better insulation adhesion
The insulation layer formed under greater pressure gives the extruded PI copper wire a tight bond. Even when twisting or bending produces large deformation, its insulation performance will not be affected. This excellent insulation adhesion ensures that the copper wire can still maintain good insulation performance in a complex mechanical stress environment.
Smooth surface and scratch resistance
The insulation layer density of extruded PI copper wire is higher, the surface is smoother, and the scratch and impact resistance is improved by 30-50%. This feature enables it to effectively resist external friction and impact in vibration environments such as automobiles, high-speed railways, and aerospace, and prolong its service life.
Wide temperature range adaptability
The operating temperature range of extruded PI copper wire is -269℃~380℃, while the wrapped type is mostly -250℃~260℃. Such a wide temperature range adaptability enables extruded PI copper wire to meet the needs of special fields such as aerospace ultra-low temperature refrigeration equipment.
Better environmental adaptability
The dense insulation layer structure enables extruded PI copper wire to more effectively resist oil pollution and acid and alkali corrosion. In harsh environments such as chemicals and ships, its life can be extended by about 20%. In addition, since there is no volatilization of residues between the wrapping layers, it is also suitable for occasions with extremely high requirements for environmental cleanliness, such as semiconductor manufacturing and spacecraft vacuum environments.
Clean and environmentally friendly
Extruded PI copper wire has a single material and high purity. No other harmful substances will be produced in either the production process or the use scenario, and it is highly environmentally friendly. However, due to the presence of adhesive layer materials, the wrapped type cannot meet the use requirements in some special occasions with strict environmental protection requirements.
The difference between “winners and losers” in high-end application scenarios
New energy vehicles: the “heart” of 800V high-voltage systems
In the field of new energy vehicles, with the gradual popularization of 800V high-voltage systems, extruded PI copper wire has become the preferred material for 800V high-voltage drive motors. It can meet the needs of high pulse voltage (>1500V) and compact space, providing a strong guarantee for the efficient operation of new energy vehicles. Wrapped PI copper wire is only suitable for low-power motors or as a backup solution, and is gradually marginalized in mainstream applications.
Aerospace: “Survival Expert” in Extreme Environments
The performance requirements of materials in the aerospace field are extremely demanding. The ultra-thin insulation and radiation resistance of extruded PI copper wire make it irreplaceable in this field. It can adapt to the -269℃ liquid helium environment and meet the working requirements of aerospace equipment under extreme conditions. Wrapped PI copper wire is mainly used in auxiliary circuits that require multi-layer protection and undertakes relatively minor tasks.
Industrial inverter: “durability king” under high frequency
In industrial inverters, extruded PI copper wire has stable corona resistance under high-frequency IGBT drive, which can significantly reduce operation and maintenance costs. Wrapped PI copper wire is more suitable for short-term overload scenarios, but there is a certain gap compared with extruded PI copper wire in terms of long-term stable operation.
Special transformer: “all-round player” in extreme environments
For special transformers, extruded PI copper wire achieves high power density with its ultra-thin insulation, and can adapt to extreme environments such as shipboard and plateau. Wrapped PI copper wire is only suitable for conventional windings of conventional oil-immersed transformers, and it is difficult to meet the needs in special application scenarios.
Cost comparison under long-term value
Economic value
The initial cost of the extruded type is only 20%-30% higher than that of the wrapped type, but its service life is 2-5 years longer than that of the wrapped type. The wrapped type needs regular inspection and partial replacement during the service life, while the extruded type is maintenance-free for 10 years. During the service life of the electromagnetic wire, the average cost of the extruded type is much lower than that of the wrapped type.
Green benefits
In terms of production energy consumption, the extruded PI copper wire adopts a continuous process with low energy consumption, and there is no exhaust gas or waste discharge during the production process, which can achieve green and environmentally friendly production. The wrapped PI copper wire adopts intermittent wrapping and requires high-temperature sintering, which has high energy consumption. Its environmental protection degree also depends on the composition of the adhesive layer material, and it is relatively disadvantaged in terms of environmental protection.
In summary, the extruded polyimide copper flat wire has its significant advantages in ultra-thin insulation, high reliability and wide temperature range. It is irreplaceable in the field of high-end equipment (such as new energy vehicles, high-speed rail, and aerospace), and is the core driving force for promoting the upgrading of electrical technology. The wrapped PI copper wire occupies a certain market share in the mid- and low-end markets and special repair scenarios by relying on its cost advantage. With the increasing popularity of 800V high-voltage systems and wide-bandgap semiconductors, TST cables’ original extrusion technology is expected to further dominate the high-end electromagnetic wire market and bring new changes to the development of the electrical industry.
If you want to learn about TST cables’ innovative product “extruded polyimide insulated flat copper wire”, please scan the QR code below and add “TST cables official customer service” to get new product information and quotes!
Also available in:
Arabic
English
Japanese
Russian
Portuguese (Brazil)