With the development of high-speed railways and urban rail transit, the demand and standards for rail transit cables are also being improved and perfected. In addition to being soft and good in bending performance, rail transit cables must also have good heat resistance, cold resistance and a certain degree of non-flammability; at the same time, they must also have sufficient ozone resistance, corrosion resistance to fuel oil, lubricating oil, etc. and chemical stability. TST CABLES’s locomotive cable material is a low-smoke, halogen-free base material, which is not only environmentally friendly but also meets customers’ requirements for non-toxic smoke in public fire safety cables.
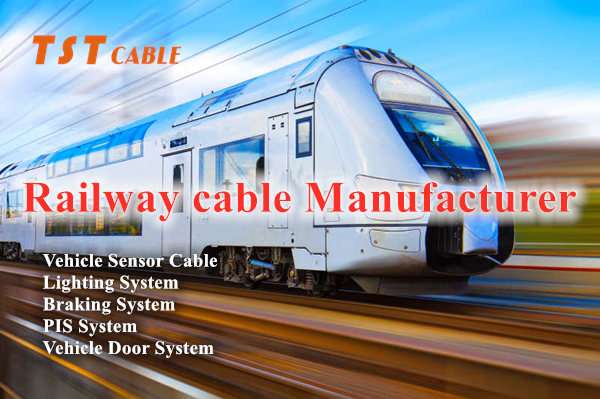
Comparison and selection points between rail transit cables and other cables
- Special requirements for coaxial cables in rail transit cables
Coaxial cables (Coaxial Cable) have unique applications in the field of rail transit, and their design must meet the following additional requirements:
Low-smoke, halogen-free flame retardant (LSZH): It releases less smoke and is non-toxic during a fire, and complies with the EN 45545 fire protection standard (such as R23/R24 grade).
Lightweight and flexible: Adapt to the compact and frequently vibrating environment inside the train. For example, the coaxial cables produced by Tester are made of lightweight materials with a small bending radius for easy wiring.
Extreme temperature resistance: The high-cold cable can withstand -40°C to +125°C (or even higher), suitable for trains running in polar or high-temperature areas.
Anti-electromagnetic interference (EMI): The shielding layer (such as copper mesh) effectively isolates the high-frequency noise generated by the motor, inverter and other equipment in the track system to ensure the stability of signal transmission. - Typical application scenarios of rail transit cables
Cable type Application examples
Power cable Traction motor power supply, train auxiliary system (lighting, air conditioning)
Control cable Signal transmission (such as braking system, door control), sensor data acquisition
Coaxial cable On-board video monitoring, radio communication (such as CBTC system), on-board broadcasting
High temperature resistant cable High temperature areas such as engine compartment and near inverter
High-cold cable Roof equipment and bogie wiring of trains in cold areas - Key parameters for rail transit cable selection
Electrical performance:
Voltage level: Rail transit power cables are usually 600V/1000V, while ordinary cables are mostly 300V/500V.
Impedance matching: Coaxial cables must strictly match 50Ω or 75Ω (such as EN50264 standard) to ensure signal integrity.
Mechanical properties:
Bending radius: Rail transit cables must meet dynamic bending requirements (such as ≤5 times the outer diameter of the cable).
Wear resistance: Pass abrasion test (such as IEC 60811-503), adapt to frequent movement scenes.
Environmental adaptability:
Weather resistance: Pass salt spray test (IEC 60068-2-11) and UV aging test (ISO 4892-3).
Fire rating: Meet EN 45545-R23/R24 (low smoke halogen-free flame retardant) or UL 94 V-0 (vertical burning test). - Domestic rail transit cable manufacturer solution
Taking TST cable as an example, its rail transit cable product features:
Covering standards: EN50264 (coaxial cable), EN50306 (data cable), EN50382 (sensor cable), etc.
TST cable innovative technology:
Thinning cable: Reduce weight by optimizing insulation thickness (such as reducing by more than 15%).
High temperature resistant material: Using silicone rubber sheath, the temperature resistance can reach 200°C.
Actual case: TST cable has passed the installation assessment of manufacturers such as CRRC and Bombardier, and is widely used in subway and high-speed rail projects. - Common problems and solutions for rail transit cables
Problem 1: Cables become hard at low temperatures, making installation difficult
Solution: Use high-cold cables (such as Test H-grade products), and add elastomers to the material formula to ensure flexibility at -40°C.
Problem 2: Signal interference affects communication quality
Solution: Use double-shielded coaxial cable (such as aluminum foil + copper mesh) and pass impedance matching test (such as VSWR≤1.5:1).
Problem 3: Long-term vibration causes loose connectors
Solution: Use self-locking connectors (such as IP67 protection level) and perform torque calibration regularly. - Future trends of rail transit cables
Intelligence: Integrate fiber optic sensors to monitor cable temperature and stress status in real time (such as based on IEC 61970 standard).
Environmental protection: Promote bio-based materials (such as PLA insulation layer) to reduce carbon footprint.
Modular design: cable assemblies with pre-installed connectors shorten installation time (such as TST SEAL’s “plug and play” solution).
Through the above comparison and selection points, it can be seen that TST cables rail transit cables far exceed ordinary cables in terms of safety, reliability and environmental adaptability, and are the core components to ensure the efficient operation of trains. When selecting, you need to combine the specific application scenarios and refer to international standards (such as EN, IEC) and mature solutions of domestic manufacturers. If you need rail transit cables, please send an email to contact TST cables.
Also available in:
English