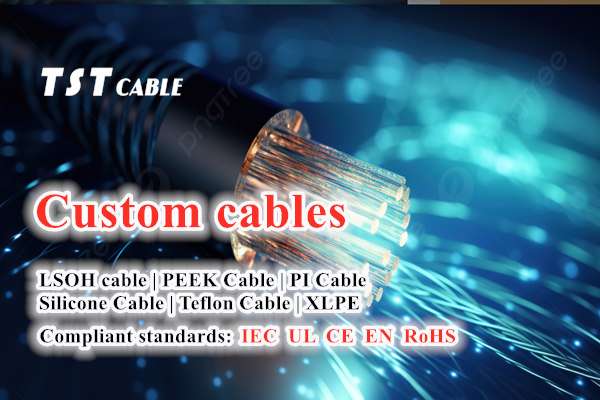
High flexible silicone cable is a special cable designed for extreme environments and high-frequency dynamic applications. Its core advantages lie in its ultra-high flexibility and excellent weather resistance.
Silicone rubber flat cable consists of a sheath, an insulator and a conductor from the outside to the inside. The sheath of the cable is designed to be a flat structure, and several conductors wrapped by insulators are evenly arranged flat inside. The sheath is made of silicone rubber material, which is not only wear-resistant, pressure-resistant, but also corrosion-resistant. Several conductors independently wrapped by insulators are evenly distributed inside, which can achieve a wire to complete multiple transmission operations at the same time, greatly improving the transmission efficiency and stability.
I. Core performance of high flexible silicone cable
- Ultra-flexibility and fatigue resistance
Material characteristics: Silicone rubber is used as the insulation layer and sheath material, combined with multiple strands of ultra-fine oxygen-free copper wire stranded conductors (such as Category 6 standards), and the bending life of the cable is significantly improved through the short pitch stranding process.
Dynamic performance: It can withstand more than 10 million repeated bends (common cables usually only 500,000 times), suitable for frequently moving scenes (such as robotic arms, drag chain systems).
Anti-torsion ability: Special structural design (such as spiral winding) allows the cable to maintain stable connection when rotating or twisting. - Temperature resistance and chemical stability
Wide temperature range: The operating temperature range can reach -60°C to +200°C (some models can reach +250°C), and can even withstand higher temperatures for a short time.
Corrosion resistance: Silicone rubber materials have excellent resistance to acids, alkalis, oil stains, ultraviolet rays, ozone, etc., and are suitable for harsh environments such as chemicals and oceans.
Low-viscosity surface: Reduce friction resistance and reduce the risk of wear of cables during movement. - Electrical and mechanical properties
High insulation: The silicone rubber insulation layer still maintains an insulation resistance of more than 500MΩ/km (at 20°C) at high temperatures to ensure electrical safety.
Anti-electromagnetic interference (EMI): Through tinned copper wire braided shielding (coverage ≥85%) or aluminum foil + copper mesh composite shielding, electromagnetic interference is effectively suppressed, suitable for high-interference environments such as inverters and servo motors.
Tensile and wear-resistant: Using polyurethane (PUR) or thermoplastic elastomer (TPE) sheath, the wear life is 3-5 times longer than PVC sheath. - Environmental protection and safety
Flame retardant performance: in line with IEC 60332-1-2 standards, with self-extinguishing properties, reducing the risk of fire.
Non-toxic and odorless: Silicone rubber materials comply with RoHS and REACH environmental regulations and are suitable for sensitive fields such as medical and food.
II. Typical application scenarios of TST CABLE high-flexible silicone cable - Industrial automation and robotics
Robot arm cable: used for the joints of six-axis robots, it needs to withstand high-frequency bending (>10 million times) and torsion.
Seventh axis cable: connected to the track mobile robot, requiring high tensile strength (≥500N) and wear resistance.
CNC machine tools: signal/power transmission between the spindle motor and the control system must be resistant to oil and high temperature (>150°C). - New energy and power systems
Photovoltaic tracking system: adapt to outdoor ultraviolet radiation (≥1000 hours), temperature difference (-40°C to +90°C) and frequent angle adjustment.
Wind turbines: power transmission between the rotor and the generator must withstand salt spray corrosion (ISO 9227 standard) and dynamic vibration.
Electric vehicles: battery management system (BMS) and charging interface cables require low temperature resistance (-40°C) and high flexibility. - Medical and precision equipment
Surgical robots: cables in joints must meet sterilization conditions (ethylene oxide or gamma ray sterilization) and sterility requirements.
CT/MRI equipment: high-frequency signal transmission cables must be resistant to electromagnetic interference (EMI) and high temperature resistance (>120°C).
Portable medical equipment: such as monitors and infusion pumps, cables must be lightweight (<100g/m) and highly flexible. - Aerospace and marine engineering
Avionics equipment: Fuel system sensor cables need to withstand aviation fuel and extreme temperatures (-55°C to +150°C).
Marine power systems: Hydraulic control cables need to resist seawater corrosion (ASTM B117 salt spray test ≥2000 hours) and dynamic bending. - Smart home and consumer electronics
Smart lamps: LED driver cables need to withstand high temperatures (>120°C) and frequent switching (>100,000 times).
Wearable devices: Flexible charging cables need to support more than 10,000 bends (radius <1mm) and lightweight design.
III. Future development trends of silicone cables - Material innovation and environmental protection upgrades
New silicone rubber: Develop liquid silicone rubber (LSR) and nano-modified silicone to further improve temperature resistance and tear resistance.
Bio-based materials: Explore plant-based silicone or degradable sheath materials (such as PLA-PUR composites) to reduce carbon emissions. - Intelligence and self-healing technology
Self-healing cable: Through microcapsule technology or shape memory materials, microcracks are automatically repaired when the cable is damaged.
Digital twin monitoring: TST CABLE integrates fiber optic sensors (FBG) or graphene coatings to monitor cable temperature, stress and wear status in real time. - High-speed data transmission and 5G adaptation
High-frequency signal cable: Optimize conductor structure and shielding design to support 5G millimeter wave (28GHz/39GHz) and Ethernet power (PoE++).
Ultra-thin flexible printed circuit (FPC): Combined with silicone cable, more compact wiring (such as internal connection of folding screen mobile phones). - Customization and rapid manufacturing
Modular design: Supports quick-plug connectors, customized lengths (±5cm accuracy) and multi-core combinations (such as 12V power supply + CAN bus + USB 3.0).
Additive manufacturing (3D printing): Directly print cable sheaths or embedded sensors to shorten the R&D cycle (<48 hours prototype). - Extreme environment adaptability
Deep-sea cables: Develop silicone sheaths with a pressure resistance of >100MPa for seabed mining or ROV (remotely operated vehicle).
Space-grade cables: Pass NASA low outgassing test (ASTM E595), suitable for satellite solar panels or Mars rovers. - Recommendations for silicone cable selection
Selection parameters Recommended standards
Operating temperature -60°C to +200°C (ordinary silicone cable); special models can reach +250°C
Bending life >10 million times (dynamic application); ordinary silicone cable can be selected for static application
Shielding requirements High interference environment (inverter, servo motor) requires ≥85% coverage of tinned copper wire braided shielding
Sheath material PUR (wear-resistant) is preferred for dynamic scenes; silicone rubber (heat-resistant) can be selected for static scenes
Certification and standards IEC 60332-1-2 (flame retardant), ASTM D2240 (hardness), UL 94 V-0 (fireproof)
Highly flexible silicone cables are rapidly developing in the direction of high performance, intelligence, and environmental protection. Their applications have expanded from traditional industries to cutting-edge fields such as new energy, medical care, and aerospace. With the advancement of materials science and manufacturing technology, more innovative products with self-healing, ultra-thin, and high-speed transmission will appear in the future, providing more reliable connection solutions for complex working conditions. TST CABLES reminds users that they need to consider temperature, dynamic load, environmental corrosion and other parameters when choosing, and give priority to brand products that have passed international certifications (such as ISO 9001, EN, CE). If you need silicone cables, please email us.
Also available in:
English