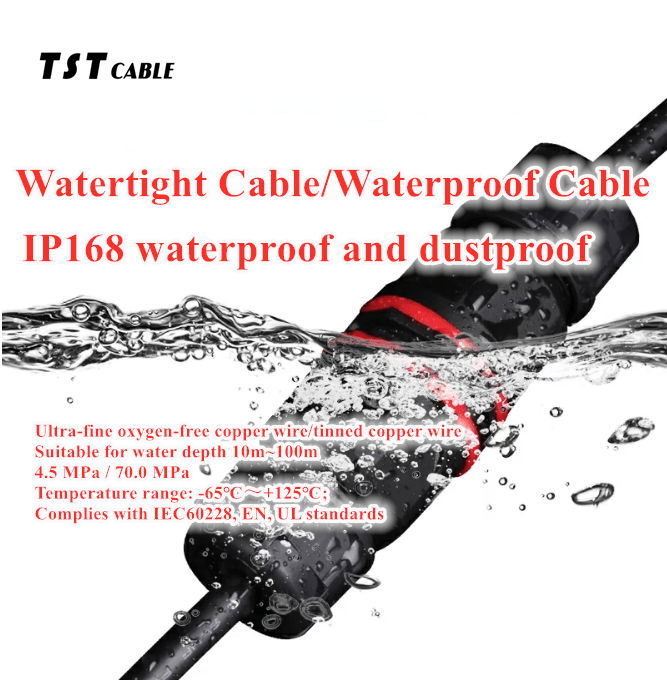
Waterproof cable/Water Resistant Cable
Water Resistant Cable is a cable specially designed to work in humid environments or in direct contact with water. This type of cable pays special attention to waterproof performance in both structural design and material selection to ensure that it can work normally underwater or in high humidity environments without affecting electrical performance. Below TST CABLES will give you a detailed introduction to the characteristics, advantages, industry applications, testing standards, manufacturing processes and technological development trends of watertight cables.
Structure of Watertight Cable
Watertight cables usually consist of the following parts:
Conductor: Usually copper or tinned copper to ensure good conductivity.
Insulation layer: Water-resistant materials such as cross-linked polyethylene (XLPE) or ethylene propylene rubber (EPR) are used to provide good electrical insulation.
Waterproof layer: Waterproof materials such as polyurethane (PU) or special synthetic rubber are used to prevent moisture penetration.
Shielding layer: Used to reduce electromagnetic interference (EMI) or radio frequency interference (RFI) and protect the internal conductor from external interference.
Reinforcement: Such as steel wire or fiber, to improve the mechanical strength and bending performance of the cable.
Sheath layer: The outermost layer of protection, usually made of oil-resistant, wear-resistant, and weather-resistant materials such as polyvinyl chloride (PVC) or polyurethane (PU).
Advantages of watertight cables
Waterproof performance: It can effectively prevent moisture from entering the cable to ensure that the electrical performance is not affected.
Durability: It has a long service life in humid or underwater environments.
Safety: Reduce short circuit or electric shock accidents caused by moisture.
Reliability: It can maintain stable electrical transmission performance even in harsh environments.
Application of watertight cables in the industry
Marine engineering: Suitable for laying submarine cables, internal wiring of ships, etc.
Water conservancy facilities: Power transmission in water conservancy facilities such as reservoirs, dams, and pumping stations.
Industrial production: Industrial environments such as chemical plants and sewage treatment plants that require water-resistant cables.
Construction industry: Electrical wiring in humid areas such as underground garages and around swimming pools.
Agricultural irrigation: Power and signal transmission in farmland irrigation systems.
Water Resistant Cable test standards
Common Water Resistant Cable test standards include but are not limited to:
IEC 60228: Standards for conductors for fixed laying.
IEC 60331: Test standard for cables to maintain circuit integrity under fire conditions.
IEC 60332: Test standard for the combustion performance of cables in flames.
GB/T 12706: Standard for extruded insulated power cables with rated voltages of 1kV (Um=1.2kV) to 35kV (Um=40.5kV).
ASTM D2240: Standard method for measuring material hardness (Shore durometer).
Water Resistant Cable manufacturing process
The manufacturing of watertight cables usually involves the following steps:
Conductor production: Copper or copper alloy is drawn into wires of the required specifications.
Insulation layer extrusion: The insulation material is evenly wrapped around the outside of the conductor using an extruder.
Waterproof layer treatment: A waterproof layer is formed outside the insulation layer by dipping or spraying.
Shielding layer winding: Use metal wire or metal tape to wrap around the outside of the waterproof layer.
Sheath extrusion: The last step is to extrude the outer sheath material and cover it on the surface of the cable.
Development trend of Water Resistant Cable technology
Environmentally friendly materials: Develop more environmentally friendly and recyclable materials to reduce the impact on the environment.
Intelligent monitoring: IoT and artificial intelligence integrate sensor technology to monitor the working status of cables and improve operation and maintenance efficiency.
Resistant to extreme environments: Research watertight cables that can adapt to wider temperature ranges and pressure conditions.
Lightweight design: New materials and new processes are used to reduce the weight of cables and facilitate laying.
Multifunctional integration: Combine multiple functions such as communication and sensing to expand the application field.
Watertight cables fully consider the importance of waterproof performance during the design and manufacturing process, and play a key role in different industries. With the continuous development of technology, future watertight cables will be more intelligent, environmentally friendly, and able to adapt to more complex application environments.
Advances in Water Resistant Cable technology
- Breakthroughs in materials science
Nanotechnology: By adding nanoparticles to cable sheath materials, their waterproof performance can be enhanced while improving wear resistance and mechanical strength.
Bio-based materials: Develop biodegradable Water Resistant Cable sheath materials to reduce the impact on the environment and achieve green manufacturing. - Optimization of production process
Continuous extrusion technology: The continuous extrusion process can improve production efficiency while ensuring the consistency and integrity of the cable sheath.
Automated detection: Introduce online detection equipment to monitor the cable manufacturing process in real time to ensure that every meter of cable meets the standard requirements.
Expansion of Water Resistant Cable industry applications
- Ocean exploration and deep-sea operations
With the development of marine science, watertight cables have been widely used in deep-sea exploration, marine observation networks, underwater robots (ROV/AUV) and other fields. These applications require cables to not only have a high degree of watertightness, but also to withstand extreme conditions such as high pressure and low temperature. - Clean energy
Offshore wind farms: With the increase in offshore wind power projects, watertight cables are used to connect electrical equipment inside and outside the wind turbine tower to ensure the reliability of power transmission.
Tidal power generation: Tidal power generation devices need to work in a state of seawater immersion, and watertight cables provide the necessary power transmission guarantee. - Intelligent transportation system
In intelligent transportation systems, such as intelligent street lights, traffic lights, road monitoring and other facilities, watertight cables can ensure normal operation in rainy days or flooded sections, ensuring traffic safety and information transmission.
Testing and certification
- Water pressure test
By applying a certain amount of water pressure to test the sealing performance of the cable, ensure that the cable will not leak water in the underwater environment. - Salt spray test
Simulate the salt spray erosion in the marine environment and evaluate the corrosion resistance of the cable under long-term exposure to salt conditions. - High and low temperature cycle test
Test the performance stability of the cable under extreme temperature changes to ensure that the cable can still work normally in cold or hot weather. - International standard certification
Obtain international certifications such as UL, CE, RoHS, etc. to prove that the product meets international safety and environmental protection requirements and enhance market competitiveness.
Further development of Water Resistant Cable manufacturing technology
- Multi-layer composite structure
Adopt a multi-layer composite structure design, combining the advantages of different materials, such as the inner layer uses a material with strong waterproof performance, and the outer layer uses a material with good wear resistance and weather resistance to improve the overall performance. - Smart production line
Introducing smart manufacturing technologies, such as robot arms and automated detection systems, to improve production efficiency, reduce human errors, and ensure product quality.
Future prospects for Water Resistant Cable technology
- IoT integration
In the future, watertight cables will be more intelligent, and may integrate sensors for real-time monitoring of cable status, and realize remote management and fault warning through IoT technology. - Repairability design
Develop watertight cables with self-repairing capabilities, which can automatically restore their waterproof performance even after minor damage and extend their service life. - Modular production
The modular design concept allows watertight cables to be flexibly combined according to specific application scenarios to meet diverse needs. - Eco-friendly
Continue to promote the application of environmentally friendly materials, reduce energy consumption in the production process, and strive to achieve zero emission goals.
Through these technological advances and innovative developments, watertight cables will not only play a greater role in existing application fields, but will also open up more new application scenarios, providing strong support for modern science and technology and social development.
[Waterproof, safe and reliable – TST CABLES leads a new era of watertight cables]
In the unpredictable natural environment, the safety and stability of power transmission are crucial. TST CABLES launches a new generation of watertight cables, using advanced waterproof technology and high-quality materials to ensure that the cables maintain excellent performance in humid and even underwater environments. Whether it is marine engineering, water conservancy projects or intelligent transportation systems, TST CABLES’s watertight cables can provide you with unparalleled protection and reliable power transmission. Let us guard every detail together and create a safer and smarter world together.
If you have customized watertight cables, waterproof cables, submarine cables, ship cables, XLPE cables, LSOH cables, UL cables, industrial cables, power cables, control cables, etc., and need further technical support or cable solutions, you can visit the TST CABLES official website, or send an email to the professional cable engineer of TST cable manufacturers at any time (email: lixiangchao@testeck.com, please state your country, your industry, your needs in the email, and we can also provide you with free samples).
Also available in:
English