What are fluorinated polymers?
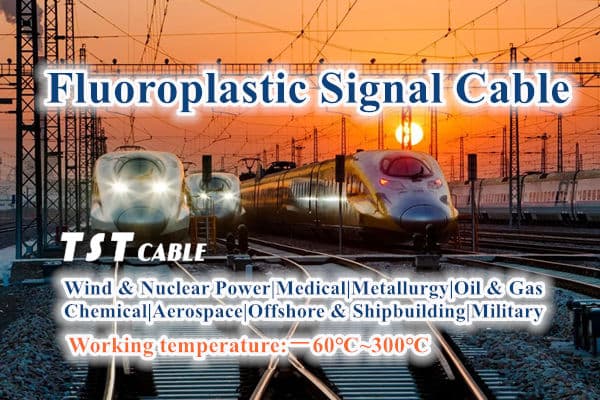
Fluoropolymers are a class of polymer materials containing the element fluorine, and they are known for their excellent heat resistance, chemical resistance, non-stickiness, low coefficient of friction, and excellent electrical insulation properties. They are polytetrafluoroethylene (PTFE), perfluoroethylene propylene (FEP) copolymers, polyperfluoroalkoxy (PFA) resins, polychlorotrifluoroethylene (PCTFF), ethylene chlorotrifluoroethylene (ECTFE) copolymers, ethylene tetrafluoroethylene (ETFE) copolymers, polyvinylidene fluoride (PVDF), and polyvinyl fluoride (PVF). Each of them has different properties and application areas. The following TST CABLES on these common fluoroplastic materials are introduced in detail:
I. History of Fluoroplastics cable
Fluoroplastics was founded in 1934, Schloffer, Scherer found polychlorotrifluoroethylene (PCTFE). 1938 DuPont’s R.J. P1unkett found polytetrafluoroethylene (PTFE) and industrialized in 1949. Following the British ICI, Germany’s Hoechst, Japan’s Daikin Industries, Italy’s Montefluos and other successive production. China’s fluorine plastic in 1958, the first successful development of industrialization in Shanghai. 80 years after the countries have increased production capacity, new varieties continue to appear, the existing varieties of more than 20 kinds, the use of the increasingly expanding.
Fluorine plastic is the initial raw material of fluorine stone (also known as coccolith CaF2) and sulfuric acid reaction generated by hydrogen fluoride. Chloroform, perchloroethylene and other chlorinated hydrocarbons are fluorinated by HF in the presence of a catalyst to produce fluorine-containing compounds. The fluorine-containing hydrocarbons obtained in this way can be thermally decomposed, dechlorinated and other reactions to obtain monomers such as tetrafluoroethylene, hexafluoropropylene, and trifluoroethylene chloride. By homopolymerization or copolymerization of these monomers, various fluoroplastics can be obtained. The performance of fluoroplastics depends on the polymerization method (such as suspension polymerization, emulsion polymerization, solution polymerization), the degree of polymerization, molecular weight distribution and post-processing process.
Second, the varieties and applications of fluoroplastics
Fluoroplastics are made from fluorine-containing monomers such as tetrafluoroethylene, hexafluoropropylene, trifluoroethylene chloride, vinylidene fluoride, fluoroethylene, hexafluoroisobutylene, perfluoroalkyl vinyl ether and vinyl and other monomers through polymerization or copolymerization reaction. The main varieties of fluoroplastics are as follows, but PTFE is the most important in terms of quantity and use.
Polytetrafluoroethylene (PTFE, abbreviated as F4) Polyperfluoroethylene Propylene (FEP, abbreviated as F46)
Fusible polytetrafluoroethylene (PFA), a copolymer of tetrafluoroethylene and perfluoroalkyl vinyl ether Polychlorotrifluoroethylene (ECTFE, F3)
Polyvinylidene fluoride (PVDF, abbreviated F2) Polyvinylidene fluoride (PVF, abbreviated F1)
Copolymer of vinylidene fluoride and chlorotrifluoroethylene (Kel-F, abbreviated F23) Copolymer of vinylidene fluoride and tetrafluoroethylene (F24)
Copolymer of vinylidene fluoride and hexafluoropropylene (vitonA, abbreviated F26) Copolymer of vinylidene trifluoride and ethylene (Halar, abbreviated F30)
Copolymer of tetrafluoroethylene and ethylene (Tefzel, abbreviated F40) Copolymer of vinylidene fluoride and hexafluoroisobutylene (CM-1)
Fluoroplastics represented by F4 have a series of excellent characteristics, high temperature resistance and long-term use of temperature up to 200 ℃; low temperature resistance in -100 ℃ is still soft, corrosion-resistant aqua regia and cut organic solvents; weather-resistant plastics have the best aging life; high insulation volume resistance of 1018 ohm-cm, and the dielectric properties of the temperature and frequency of the change is almost irrelevant; high lubrication with the smallest coefficient of static friction in plastic High lubrication has the smallest coefficient of static friction among plastics; non-adhesion has the smallest surface tension among solid materials and does not adhere to any substance; non-toxic with physiological inertia, suitable for contact with blood. Because of the above practical properties of fluoroplastics, it can be used in many areas of the national economy. Such as chemical anti-corrosion pipeline and equipment on the lining and coating, ultra-pure material over the L material, high and low temperature resistant hydraulic transmission hose, resistant to a variety of harsh environments of the sealing gaskets, low-friction bridge expansion slider, all kinds of oil-free lubrication piston ring, high temperature and high frequency electronic instruments, insulation, flexible cables, high-level printed circuit boards, the thermal performance of the compression voltage materials, oil-free cooking and drinking utensils, mold coating, human blood vessels and heart and lungs The use of the material in these fields is only a representative example of its use. It is fully believed that with the progress of processing technology, there will be more fluoroplastic products applied in various sectors of the industry.
When discussing the physical properties of fluoroplastics, it is known that fluoroplastics, due to its high fluorocarbon bonding energy and the shielding effect of fluorine atoms, have excellent chemical resistance, dielectric properties, weather resistance, non-flammable and non-sticky, low coefficient of friction and a wide range of temperatures and other properties, and therefore are widely used in corrosion resistance, sealing, load bearing, anti-adhesion, electrical insulation, medical and health care, and household goods, etc. It has become one of the indispensable materials in modern advanced science, defense industry, electrical and electronic, chemical and mechanical industries. Fluoroplastics are widely used in anti-corrosion, sealing, load support, anti-adhesion, electrical insulation, medical and health care, household goods, etc. They have become one of the indispensable and important materials in modern cutting-edge science, national defense industry, electrical and electronic industry, chemical industry and mechanical industry.
Fluorine plastic occupies a small proportion in the whole plastics, but it is an indispensable variety in the process of realizing the four modernizations in China. With the continuous development of economic construction, fluorine plastic will certainly gain rapid development.F4 corrosion-resistant piping and its fittings F4 piping can be used as a pipeline to transport corrosive or viscous liquids, but also as a corrosive gas pipeline, exhaust pipe and steam pipe. Because of the low mechanical strength of F4, poor pressure resistance, large coefficient of linear expansion, and, its mechanical strength due to the temperature and reduce the deformation is easy, especially when subjected to high temperatures and high pressures, the contradiction is more prominent, so the F4 pipe and pipe fittings must be reinforced with glass fiber reinforced plastic or metal pipe. The connection between them all adopts F4 pipe belongs to tight lining pipe, that is, FRP and F4 pipe bonded into a whole. It can overcome the problems caused by different coefficients of linear expansion between different materials, and can be used as the transmission pipeline of the negative pressure system, and can prevent the corrosion of the pipeline by the atmosphere and the environment. As some fluids in a certain flow rate and the wall of the pipe wall often friction, easy to generate static electricity and lead to wall breakdown, should take the potential of the same conductive measures to prevent, or in the molding of the inner tube and its fittings when adding an appropriate amount of carbon ink, in order to prevent the generation of static electricity and to reduce the thermal expansion and contraction of the size caused by the change in size.
Third, the characteristics of fluoroplastics in detail
Fluorine plastic has heat-resistant, cold-resistant, weather-resistant, drug-resistant, solvent-resistant, excellent insulating properties and high-frequency electrical properties. And has no wither, self-lubrication, low friction coefficient and other characteristics.
Polytetrafluoroethylene, perfluoro (ethylene-propylene) copolymer (FEP) is composed entirely of carbon and fluorine atoms, while polyvinylidene fluoride (PVDF), polyvinylidene fluoride (PVF) molecules also contain hydrogen atoms, and polytrifluoroethylene also contains chlorine atoms. The excellent performance of fluoroplastics is realized by the high binding energy between carbon and fluorine atoms. The backbone of the main chain of PTFE is carbon atom, which is completely surrounded by fluorine atoms, so it has the highest performance, while PFA, FEP, ETFE and other varieties of softening point is lower than PTFE due to the influence of the side group, and other properties are also changed.
- Thermal properties: Fluorine plastic has flame retardant and excellent heat resistance. PTFE and PFA continuous use temperature up to 260 ℃, short-term can be used at 300 ℃, FEP use temperature is 60 ℃ lower than them, PCTFE can be used at a maximum of 120 ℃. Fluoroplastics such as long-term use at high temperatures will cause changes in crystallinity, especially in the manufacture of equipment lining.
- Drug resistance: Fluoroplastics have excellent drug resistance and solvent resistance, especially PTFE, PFA, FEP, etc., acid, alkali, solvents on them are not leaching. But the molten alkali metals, fluorine, chlorinated hydrocarbons have different degrees of influence on them, PCTFE, ETFE, PVDF, etc. in the fluoroplastics drug resistance is slightly worse, but much better than the corrosion resistance of other plastics.
- Electrical properties: the electrical properties of fluoroplastics, especially the high-frequency electrical properties of other materials is difficult to match. PTFE, FEP, PFA molecular polarity is very low, in a wide range of temperatures, frequency interval changes are very small, the relative dielectric constant is stable, the dielectric loss is very low, excellent electrical insulation. Among them, PVDF also has special piezoelectricity and pyroelectricity, can be used to manufacture piezoelectric materials.
- Mechanical properties: fluorine plastic molecules containing hydrogen, chlorine atoms increase its tensile strength is also improved. The embrittlement temperature of PTFE and PCTFE is very low, showing excellent low temperature performance. PTFE has the lowest coefficient of friction and exceptional self-lubrication. However, PTFE has its own disadvantages such as high abrasion and cold flow. Can be used to fill a variety of fillers to improve wear resistance, to overcome the cold flow.
- Non-sticky: Fluorine plastic has special non-stick. Especially like PTPE, FEP, PFA and other molecules with high fluorine content, the surface contact angle is very large, so that the liquid on the surface of fluoroplastic products into a ball. It is not easy to bond with resin, so it is often used to make cookware surface non-stick Xu layer.
- Weather resistance: all varieties of fluoroplastics have excellent weather resistance, even in harsh temperatures under prolonged exposure to the sun, its various properties are unchanged.
- Hydrophobicity: Fluorine plastic has a low water absorption rate, especially PTFE. It can be utilized to manufacture water-repellent composite fabrics and other equipment that are impermeable to air.
Fourth, the detailed use of fluorine plastics
Polytetrafluoroethylene is currently the largest amount of fluoroplastics in the species, accounting for about 60% of its total demand, its excellent performance, trusted by users. Other fluoroplastics are also expanding their applications in semiconductor, medical and wire covering fields. The uses of fluoroplastics can be summarized as follows:
- The use of its drug resistance: fluoroplastics in the drug resistance of the application has long been not limited to the manufacture of seals, gaskets, fittings, in other parts that require corrosion-resistant (such as piping) on the use of the star is also increasing. With the advancement of raw materials and processing technology, fluoroplastics molding methods and expand the range of factory options: such as injection molding can significantly improve production efficiency, small batch production can be used in the cutting process, PTFE bonding and welding technology development to make large-scale storage tanks and equipment lining has the possibility of FEP powder coating process to make the process more flexible and convenient. Semiconductor production process to prevent corrosion and pollution has been more fluoroplastics.
- Mechanical industry: PTFE has a small coefficient of friction, and its static coefficient of friction is lower than the dynamic coefficient of friction, so it can be used in the field of low-speed and high-load, such as in civil engineering, chemical industry, bridges and other structural components to solve the expansion and contraction problems caused by thermal expansion and vibration. Specific applications are:
(1) Bearing bushings for anti-pollution machinery (e.g. textile, paper, pharmaceutical, food machinery);
(2) Machinery for conveying non-lubricated liquids such as alkali and solvent (e.g. mixer, dyeing machine, pump);
(3) In acid, alkali and other corrosive environments (such as electroplating bath chemical equipment) under the work of the sleeve;
(4) Prohibited oil lubrication (such as oxygen equipment);
(5) meta-oil lubrication (such as ultra-low temperature freezers, liquid fuel pumps);
(6) Oil lubrication effect of poor environment (plus high temperature dryer, furnace table lunch, furnace conveyor belt) work of the sliding parts;
(7) Sliding parts under low speed and high load (movable support).
- Electrical field: Fluorine plastic is a flame retardant material, high critical oxygen index and corrosion resistance, can be used as insulation for electric wires.
ETFE, PVDF insulation resistance, insulation strength are high, mechanical strength is also excellent, can be used for computer, communication machine cable. The use of its weather resistance, irradiation resistance and other characteristics can be used for oil wells and nuclear reactors small cables. The use of its high-frequency relative dielectric constant and dielectric loss are low can be used for communications equipment, high-frequency electric instrumentation, PTFE and carbon black, carbon fibers such as conductive substances can be used as a mixture of anti-static materials and heating element materials. PVDF can also be made into piezoelectric components used in the radio industry and instrumentation industry.
- Non-stick: The use of fluoroplastics non-stick can be manufactured kitchen equipment (such as non-stick pans, snack molds), high-level buildings, exterior wall coating, foam molding molds, photocopier rollers and so on. In addition to artificial blood vessels, heart valves and other medical soil engineering materials, gas separation membrane, waterproof and breathable composite fabrics and other aspects of the use is also increasingly widespread.
V. Fluorine plastic molding characteristics
- Polytetrafluoroethylene (PTFE, F4) macromolecule carbon chain with electronegative fluorine atoms on both sides of the strong, can not be processed by ordinary thermoplastic injection molding methods to process molding, because it is almost non-fluid under the melt. Polytetrafluoroethylene is generally used in compression molding methods, can also be used in plunger extrusion molding. The resin obtained by dispersion polymerization can be extruded and calendered by paste. The specific process conditions are: pre-molding pressure with the shape of the product, size varies, but usually 9.8 ~ 34.3MPa, plus filler resin using 29.4 ~ 93MPa, for the pressurized direction of the thickness of about 600mm of the large blanks also need to have 20 ~ 30min of holding time.
In PTFE molding there will be sintered blanks into the preheated to the sintering temperature of the mold, one side of the pressurization, cooling of the hot press method; two-way extrusion of the automatic compression molding method, as well as the use of fluid pressure isobaric molding method.
Extrusion molding is a method of making rods, tubes and profiles from PTFE pre-sintered material. Usually divided into vertical or horizontal two kinds, but due to the horizontal production tube material filling is not uniform, so more vertical extrusion process. The process conditions are as follows:
① The diameter of round bar is from 13 to 40mm, the size of mold is from 15.1 to 46.0mm, the heating length is from 500 to 1100mm, the heating temperature is from 400 to 350℃, the cooling length is from 150 to 200mm, and the extrusion speed is from 4 to 1m/h.
② The diameter of the pipe is Φ15~Φ40/Φ8~Φ25, the size of the inner diameter of the cylinder and the outer diameter of the mandrel is Φ16.5~44.5/Φ8.9~27.8, the heating length is 350~800, the heating temperature is 400~350 ℃, the cooling length is 150~250mm, and the extruding speed is 3.8~1.4m/h. The direction of the development of the PTFE extruding technology is Further increase the extrusion speed and one-time molding multi-root products.
Dispersed PTFE usually paste extrusion molding method, the first will be dispersed PTFE resin and extrusion additives such as crude solvents, gasoline (b.p. for 90 ~ 120 ℃) or white oil mix, put in glass or stainless steel bottle rolling 30 minutes, so that it is uniformly dispersed and absorbed, placed in the 8 ~ 12h, pressed into a blank placed in the extruder cavity, the pressure of 0.69 ~ 3.43MPa pressure holding time of 30 ~ 60 seconds. ~Pressure 0.69-3.43MPa holding time 30-60 seconds. The extrudate made by this process needs to be dried in a continuous drying furnace (100-300 ℃) to remove the extrusion additives. Then into the sintering furnace sintering (360 ~ 380 ℃) sintering and rapid cooling can be obtained after a good product.
After the paste is extruded into small rods (Φ10~Φ30), it can also be sent to calender for calendering before sintering, which is the so-called raw material tape products. Specific molding conditions are 100 parts of resin, 27 parts of additives, compression ratio (R, R) 30, head temperature 50 ℃, the shape of the extruded product 50 × 14mm, calendering roller diameter of 500mm, roller temperature of 70 ℃, calendering speed of 28m/min, calendering into a 500 × 0.1mm of the raw material tape.
- Fluorine resin other than PTFE can be used thermoplastic resin molding methods such as molding, transfer molding, injection, extrusion, blow molding and so on.
Molding method: This is an old plastic molding method. It is suitable for the production of round bars, plates, tubes and other products with simple shapes and small batches.
② Transfer molding method: Transfer molding is a method of molding products by closing the mold and then squeezing the formed profile fat from the trough into the mold with high pressure. Fluorine plastic transfer molding is suitable for the production of small batches of large valves, pumps and other products. Transfer molding can be molded high-precision products, the disadvantage is that raw material consumption is large, the molding pressure used is usually below 9.8Mpa, the processing temperature is similar to the temperature of injection molding.
Injection molding; injection molding is the same as the usual plastics. It is suitable for processing carriers, instrument connectors, sockets, pipe fittings, bobbins, shaped bearings, valves, pump housings and impellers, and many other products.
Extrusion molding: Extrusion molding is suitable for molding films, tubes, rods, monofilaments, wire covers and other products.
Fluorine-containing copolymers in the molding process will release a trace of monomer and thermal decomposition, so the equipment and molds have corrosion-resistant requirements, generally using gold-containing materials such as H-alloys and other manufacturing.
Fluoroplastic coating molding dispersion coating, body coating, electrostatic coating body coating, flow impregnation and other methods. Whichever method is required to degrease, wash and roughen the surface of the substrate for sandblasting.
The thickness of the coating can be repeated until the desired thickness is reached (current level: 0.35mm/time, final thickness 2mm). Fluoroplastic products can be secondary processing, the processing conditions are: cutting speed: the diameter of the processed parts in the 200mm ~ 500mm, 200r / min or less, the cutting speed of the processed parts in the diameter of 200mm ~ 500mm, 200r / min or less. Cutting speed: when the diameter of the workpiece is 200mm to 500mm, the cutting speed is below 200r/min, when the diameter is below 50mm, the cutting speed is 750 to 800r/min. The front angle of the lathe tool should be greater than 20° to 45°, and the amount of feed should be 0.5mm/r for roughing, and 0.01mm/r for finishing.
VI. Classification of various fluoroplastics
- Properties and uses of polytetrafluoroethylene (PTFE, F4)
PTFE is one of the best materials in the world for corrosion resistance, so it is known as “King of Plastics”. It can be used in any kind of chemical medium for a long time, and its production has solved many problems in the fields of chemical industry, petroleum and pharmaceutical industry in China. PTFE seals, gaskets, sealing washers are made of suspension polymerization PTFE resin molding process. Polytetrafluoroethylene and other plastics compared with chemical corrosion resistance and excellent temperature resistance, it has been widely used as sealing materials and filler materials.
Performance: high chemical stability and excellent chemical resistance, such as resistance to strong acids, strong alkalis, strong oxidizing agents, etc., outstanding heat, cold and friction resistance, long-term use of the temperature range of -200 ~ +250 ℃, there is excellent electrical insulation, and not subject to the influence of temperature and frequency. In addition, it is non-stick, non-absorbent, non-combustible and so on. Suspension resin is generally used in molding, sintering methods of molding processing, the resulting rods, plates or other profiles can also be further processed by turning planing, drilling, milling and other machining methods. The rods can be further processed by turning, drilling, milling and other machining methods. The rods can be made into oriented films by turning and drawing.
Main applications: can be made into tubes, plates, rods, films and bearings, gaskets and other parts, widely used in the electrical and electronic industry, chemical industry, aerospace industry, machinery industry, national defense industry and so on.
- Perfluoro(ethylene-propylene) copolymer [FEP,F46].
FEP is a copolymer of TFE and hexafluoropropylene (HFP). It is also a fully fluorinated fluoroplastic, so its resistance to chemical media is no less impressive. Like PTFE and PFA, FEP has excellent insulating properties. Combined with its flame retardancy, low smoke generation, and ease of processing, FEP is an ideal material for insulating local area network (LAN) cables. With a maximum resistance of 205°C, it can be used for heating cables, thermocouples, and automotive high-temperature cables.
- Introduction to Fusible Polytetrafluoroethylene (PFA)
Also known as “perfluoroalkoxy fluoroplastics”, with PTFE, is also a perfluorinated fluoroplastics, which maintains all the excellent properties of PTFE. Unlike PTFE, PFA can be melt-processed at lower temperatures. Of course, PFA is more expensive, so it is usually used only for special heating cables, thermocouples, and high-temperature cables for automobiles.
- Ethylene-tetrafluoroethylene copolymer [ETFE, F40]
It is the toughest fluoroplastic with excellent resistance to abrasion and wear. ETFE can also withstand high temperatures up to 150°C, and cross-linked ETFE can withstand high temperatures up to 200°C. It is also the most difficult to process. It is also one of the most difficult fluoroplastics to process, ETFE is mainly used in wire and cable that need to be flame retardant, low fuming, resistant to chemical media, as well as scuff and abrasion resistant. Such as automotive, aviation cables and heating cables.
5.Introduction of Trichloroethylene Copolymer [FEVE]
FEVE organic solvent-based fluorine coatings appeared in the 80s is the epoch-making invention of fluorine coatings. In order to overcome the lack of thermoplastic fluorine resin coatings, the United States in the 80’s, Japan has developed a fluorine resin containing hydroxyl and other functional groups, can be in the low-temperature baking cross-linking curing (cross-linking of amino resins) and room temperature cross-linking curing (cross-linking of urethane). FEVE fluorine coatings in the room temperature, can be brushed, rolled, sprayed and other common coating methods, coated in a variety of substrates on the surface, not only weathering, and excellent solvent resistance, acid and alkali corrosion resistance is excellent, It not only has excellent weather resistance, but also has excellent solvent resistance, acid and alkali resistance, etc. It can also improve pigment dispersion and solvent solubility, which makes fluorine coatings have excellent decorative properties, and greatly expands the scope of fluorocarbon coatings, and makes the use of fluorocarbon coatings in daily life possible.
In the 1980s, FEVE fluorine coating products of Japan Asahi Glass (trade name LUMIFLON) began to be widely used in the fields of aircraft, cross-sea bridges, shinkansen trains, transportation vehicles, architectural steel structures, outdoor large-scale structures, etc. In 1983, the Science and Technology Commission of Dalian Municipality began to take FEVE fluorine carbon coatings as a key scientific and technological research project, and after 13 years, it was developed into a new fluorine carbon coating product with China’s independent intellectual property rights and patented in 1995, which has been used in many countries. After 13 years, in 1995, we developed the FEVE fluorocarbon coating production technology with our own intellectual property rights and national patent (Patent No.: CN1145386), which was successfully industrialized by Dalian Mingchen Zhenbon Fluorocarbon Coatings Company Limited in 1998, and was sold under the registered trademark of Zhenbon, making China the third company that can produce FEVE fluorocarbon coatings after the U.S.A. and Japan. (ZEBON), making China the third country in the world after the United States and Japan that can produce FEVE fluorine resin and reduce the cost of fluorine resin coatings, forming a series of products suitable for the exterior of buildings, steel structures, bridges, automobiles, vehicles, wood, windows and doors, curtain walls, petrochemicals, plastics, furniture and home appliances and other industries and widely used, pioneering a wide range of fluorine resin coatings, so that fluorocarbon paints are inexpensive and high quality became a reality.
- Polyvinylidene fluoride [PVDF, F2] characteristics and uses
Polyvinylidene fluoride is a crystalline polymer, low melting point, about 160 ~ 170 ℃; high mechanical strength, with abrasion resistance, cutting resistance, high temperature resistance, corrosion resistance, good electrical properties, (characterized by high dielectric constant). Also has excellent weather resistance, ultraviolet resistance, radiation resistance and processing properties; at the same time, has a low processing temperature, melt flow is good, can be made into tubes, plates, rods, films and fibers. Soluble in some organic solvents.
Mainly used for: ① Ideal anti-corrosion materials for chemical equipment, especially suitable for the use of acids, organic solvents, halogens and their mixtures. ② widely used in electronics, electrical industry, such as for electronic computer wires, aviation wires and geophysical cables, such as phi casing. ③ As the outer coating of optical fiber, high dielectric constant capacitor film and electrical tape.
7.THV Fluoroplastic Brief Introduction
It has excellent chemical resistance and electrical properties. It is the softest fluoroplastic, its electrical properties are not suitable for high-speed data communication network (i.e. Category 5 cable) in the preferred insulation, but in those places where flexibility is required, it has its unique advantages. In addition, THV can be used where bonding to other materials is required. THV can also be used in fiber optic cladding due to its excellent optical properties.
Fluoroplastic materials are widely used in cable materials, widely used in medical, marine, nuclear power, wind power, rail transportation, aviation, military, construction and other fields, if you have any questions about fluoroplastic materials and applications, please feel free to send an email to communicate with us.
Also available in:
English